In gravity diecasting, coatings can be used to present die wear and control metal solidification rate and direction
Modern Casting, March 2007
Reprinted with permission from the American Foundry Society
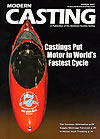
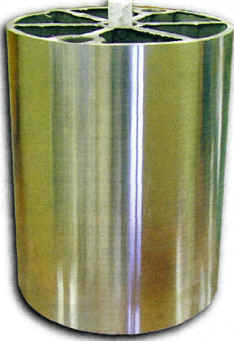
Each casting must be machined, polished and black anodized before it's put to use on the high-speed printing machine.
|
An offshore company in the printing industry had plans to manufacture a new, high-speed printer that was faster than any machine it had produced before. But the success of the project hinged on the casting of an 80-lb., aluminum structural cylinder to high quality standards. The end result would have to pass x-ray, fluorescent dye penetrant and pie-machining qualifications to ensure it had no defects. The purity requirements exceeded x-ray specifications.
Reliable Castings Corp., Cincinnati, was interested in the project, but felt the only way to achieve the metallurgical properties required was to cast the part in a tilt-pour permanent mold machine. By tilting the mold as the molten metal is poured, the metalcaster can control the turbulence of the metal flow, which reduces oxide inclusions and trapped air in the casting. Unfortunately, a tilt-pour machine that would accommodate this particular project did not exist.
Unwilling to give up on the potential sale, engineers at Reliable started brainstorming what they would need out of a tilt-pour device to be able to cast the part. A sketch was drawn up in a preliminary meeting and converted into a 2-D computer file. Reliable sent the drawings to CMH Manufacturing Co.-Hall Machine, Lubbock, Texas, a manufacturer of metalcasting equipment with an emphasis on aluminum tilt-pour permanent mold casting. CMH, having built custom casting machines for metalcasting facilities around the world, was a willing partner with Reliable on the new design.
The aluminum cylinder required 11 shell cores, and it was this core assembly that caused the difficulty in using existing tilt-pour devices. The assembly weighed nearly 100 Ibs. and could not be placed horizontally into a mold half with consistency or ease. Instead, Reliable wanted to set the core vertically on a base plate in the middle of the two mold halves with both halves closing over the core. Existing equipment had no base plate for cores and featured only a single moving platen.
The final design for the tilt-pour device used CMH's existing 3HS frame and base system to develop a dual ram system that included the core base insert, two moving platens and a counterweight to ease the tilting of the machine. The new device also required CMH to depart from its standard slide and way bar system to linear ways and bearings for a stable ram close.
With the device, Reliable was able to successfully cast the structural cylinder to all the requirements. Currently, the product is in the sampling and testing process at the customer's facility. When in full production of 1,200 pieces/yr., the castings will be machined, polished and black anodized before they are put to use.
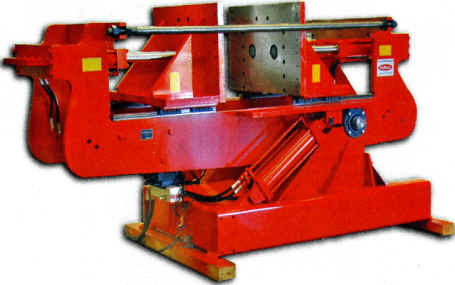
The custom-designed tilt-pour device from CMH Manufacturing
features two movable platens and linear ways and bearings for
a stable ram close.
John Hall is the president of C.M.H. Manufacturing.
www.cmhmfg.com |